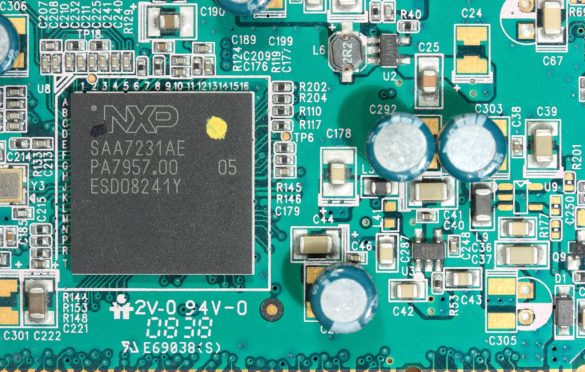
The Importance of Copper In a PCB
When it comes to PCB (printed circuit boards), there are all sorts of different types to consider. These devices are used in nearly all electronic devices—from cell phones to radios to computers and beyond—and they come in various thicknesses and in a variety of materials.
One such element used in the construction of PCBs is copper. Continue reading to discover why copper is such a great option in designing PCBs for your manufacturing needs.
Table of Contents
Benefits of Using Copper in PCBs
Stated by a pcb manufacturing company, PCBs can be made from resins, epoxy laminates, aluminum backings, and more, depending on the need. Sometimes what is required will be a thicker, more rigid board, while other times, a more flexible one will be on the docket—and these factors will help dictate what type is required.
Compared with other substances, however, using copper in your PCBs offers several advantages. These include the following.
Conductivity
Copper provides improved electric and thermal conductivity over most of the other metals that could be used so that heat can transfer through the circuit very evenly. The even transfer of heat is essential here because uneven heating could put stress on the PCB, potentially damaging your other components.
As mentioned, copper also has quite impressive electric conductivity, meaning it transmits signals with as little electrical energy loss as possible.
Efficiency
Due to its conductive properties, each copper PCB will require minimal amounts to function properly. A single ounce of copper can make for a 35 micrometers thick layer, which gives you plenty to cover a whole square foot of a board’s substrate.
Accessibility
This one is simple: copper is highly available, so it’s less expensive when compared to other metals.
Reliability
Copper is also great because it has a thermal resistance to it that is utterly unmatched. This can increase the reliability in electronic devices utilizing these boards that may need to operate in harsh environments—including those with higher temperatures.
Money-savings
Who doesn’t love to save money? This is especially helpful when you’re operating a company, trying to keep costs down so you can continue making a profit and growing your business—plus, of course, paying your employees.
Thanks to copper’s ability to evenly transfer heat, PCB manufacturers have the option to install heat sinks onto boards’ surfaces or even build boards with one side entirely covered by a thin layer of copper (also acting as a heat sink). Regardless of the method you choose to put together your PCBs, by using copper, you will likely find you’re able to cut the assembly process short and significantly reduce your team’s manufacturing expenses.
It’s Time You Strongly Consider Copper When Developing PCBs
For all the reasons above and more, if you’re in the business of making PCBs, copper is sure to be one of your new best friends. Investing in this material for the construction of your company’s boards will render happier employees and more satisfied clients and customers when production goes faster and there is a spike in product quality.
There’s no time to waste—if you aren’t already creating copper-based PCBs, it’s time to switch over or at least start incorporating them into your procedures.